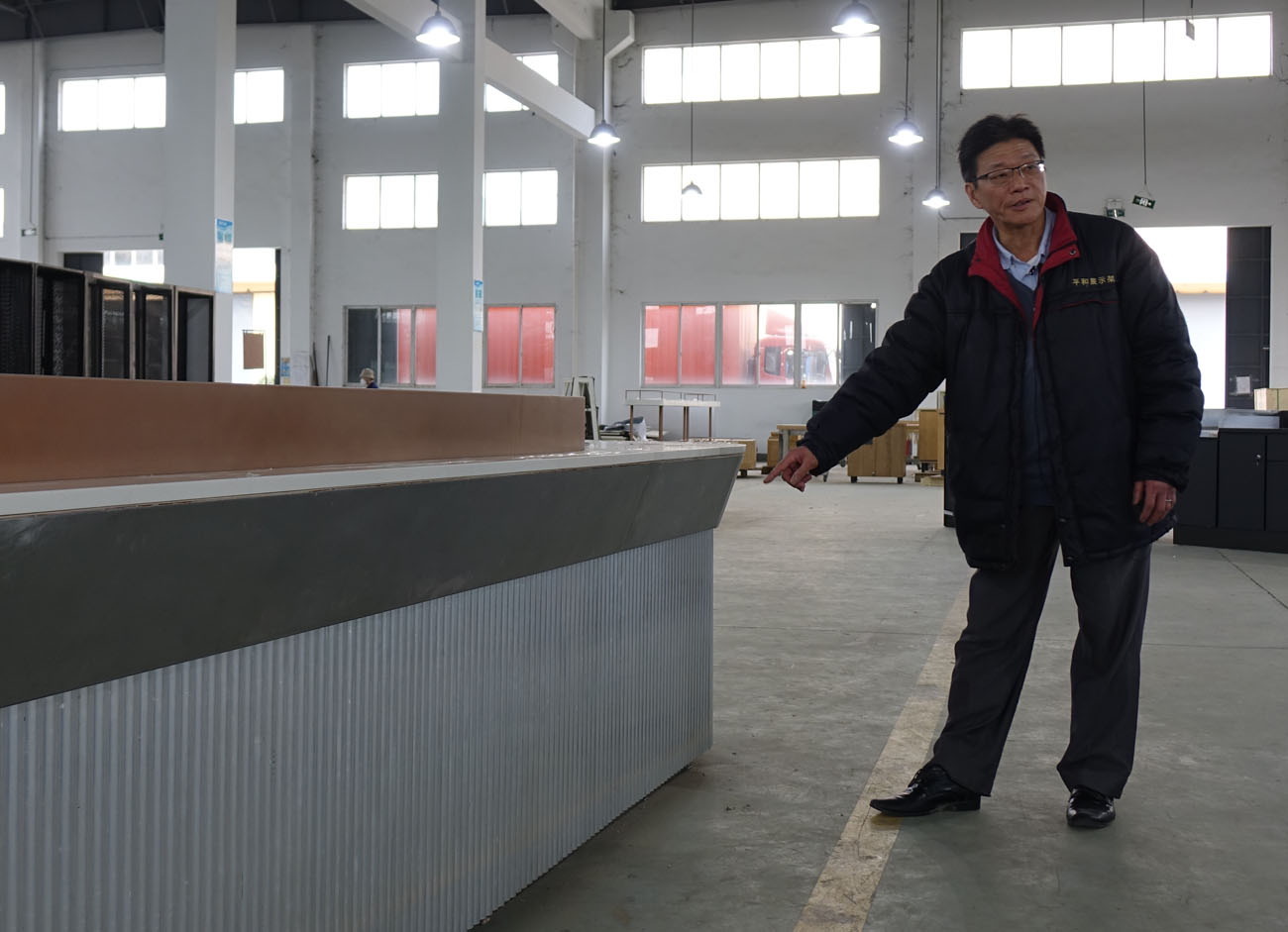
David Jones’ Recognition – How ABBACREDO Complete the Challenges of the Upmarket Department Store Display Fixtures
Customers Well Recognize the Quality of ABBACREDO’s Display Racks
ABBACREDO took orders for David Jones display racks in 2017. So far, we have successfully delivered five department stores’ display racks. Customers are genuinely satisfied with the products we have provided and hope to continue this cooperation. It is never easy to accomplish such tasks with punctuality because dedicated project management and full collaboration between various divisions are necessarily required.
There are three main challenges in this case:
Highly Composite Materials
Customers designed the display stands very beautifully with intrinsic details. The materials used are highly diverse (including metal and wood combined with LED lights, acrylic, mirrors, glass, etc.). The structure of display stands is undoubtedly much more complicated than usual, which makes this project one of the more difficult brands we have ever done.
Surface Treatment Diversity
David Jones has high requirements for the quality of its department display equipment; even the same style of display stand is designed with multiple different finishes to suit the retail space at its best. If the on-site production management is not diligently strict, it may easily cause production confusion or errors, which leads to demonstrate the importance of project management.
Short Production Lead Time& High-Quality Requirements
The customer requires the production delivery time of about 6 to 8 weeks, and there are nearly 100 styles of products. In the case of orders with many constraints and requirements, diligent project management and close cooperation amongst various divisions involved are essential. ABBACREDO team constantly challenges ourselves and always raises the quality requirements to the next level, which is indeed one of the reasons customers appreciate us as a quality supplier who aims to outdo itself every time.
Team Work that Made It Happen
Because David Jones’ order is complicated and diverse, it is necessary to understand the customer’s display drawings in detail during the quotation step. Upon receiving the confirmed order, the display’s product materials, specifications, structure, and illustrations were quickly apprehended. Then we produce manufacturing drawings and proceeded with color samples. After customer confirmation of color samples, we can arrange material purchasing immediately to facilitate production and meet quality and delivery requirements. Again, none of these steps were skipped nor looked at lightly.
Lesson Learned and Kept Improving until Perfection
When taking David Jones’s department display orders, it was inevitable to encounter some quality issues during production. But after internal brainstorming and or patient discussions with customers, there were solutions and improvements, such as:
1) When installing acrylic shelves (or glass shelves) into the back panel’s grooves, we must design the notch at corners of the inserted side of an acrylic panel. It helps in keeping acrylic shelf length long enough to reach two ends without the grooves limiting in the back panel and also preventing the acrylic panel from cracking during installation.
2) For jewelry display stand, the original design was to glue the LED extrusion frame around the top of the internal glass showcase. But we made some changes by separating the metal frame of LED from the glass showcase. The advantage of this modification was to avoid the original design of glue marks on the bonded LED metal frame and glass cover. It made the jewelry showcase more beautiful and appealing visually.
3) Per original drawing from the client, it is 90-degree for the L-shaped angle steels for griping glass shelves, but it would cause sagging after inserted glass shelf due to glass weight. We modified the L-shaped angle to be 89-degree for the upper one and 91-degree for the lower one, so it could have 1-degree uplift to keep the glass shelf level after installation without sagging due to weight.
4) One of the display fixtures drawings required the finish color of the metal frame between bronze and gold by electric plating. However, the requested color failed to be done by the electrical plating method. Per our experience in producing diverse and small quantity metal store displays, ABBACREDO had developed a new technique of painting on metalwork. We made the color sample between bronze and gold color by painting technique instead of electric plating and presented the outcome to the customer. It was pleasantly approved,so the finish was applied to mass production for related display racks and shipped out promptly.
Recognition from Customers is our Greatest Motivator
People have known that David Jones has extremely high-quality requests for display stands. Many suppliers are unwilling to take the order because they are afraid to fail the near-perfect quality requirements, which might cause lots of claims after shipment. ABBACREDO team always would like to accept challenges and continuously improve the processing technology level to meet the strict requirements. David Jones’ recognition is a great honor to the ABBACREDO team.